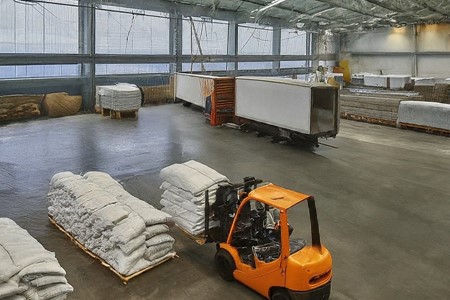
In today’s fast-paced industrial landscape, having a robust supply chain is crucial to maintaining consistent production, ensuring product quality, and staying competitive. For manufacturers, particularly those dealing with raw materials such as chemicals, metals, or agricultural goods, a strong supply chain can make the difference between thriving and struggling. Let’s explore the key components of building a resilient and efficient supply chain for raw materials, with a focus on critical steps and strategies to ensure long-term success.
1. Understanding Supply Chain Dynamics
Before diving into strategies, it’s essential to understand the dynamics of your supply chain. A typical raw material supply chain involves suppliers, manufacturers, logistics providers, storage facilities, and end-users. Each of these players must work in harmony for the entire process to function smoothly. For industries like chemical manufacturing, disruptions at any point in this chain can lead to delays, increased costs, and compromised product quality.
Building a supply chain tailored to your industry’s specific needs is the first step. Whether sourcing LR-grade chemicals like sodium oxalate, ammonium acetate, or mono ammonium phosphate, understanding how your suppliers operate is essential to ensuring consistent availability of these materials.
2. Supplier Selection and Diversification
One of the critical aspects of building a strong supply chain is carefully selecting suppliers. Reliability, reputation, and proximity to your manufacturing plant are key factors to consider when choosing suppliers of raw materials. For instance, sourcing chemicals from reputable suppliers ensures compliance with industry standards and reduces the risk of contamination or subpar quality.
To further strengthen the supply chain, diversification is essential. Relying on a single supplier for critical raw materials exposes your business to unnecessary risks. Geopolitical tensions, natural disasters, or operational failures could interrupt supply from one source. Instead, creating relationships with multiple suppliers, ideally from different regions, can help mitigate such risks.
3. Inventory Management and Forecasting
Efficient inventory management is crucial for avoiding raw material shortages or overstocking. Maintaining optimal inventory levels helps reduce carrying costs while ensuring materials are always available for production.
Modern inventory management systems with real-time tracking and automated restocking alerts can significantly enhance this process. Additionally, accurate demand forecasting allows businesses to plan better for fluctuations in production requirements, ensuring that raw materials are ordered well in advance and avoiding production delays.
For industries that deal with perishable or sensitive materials like certain chemicals, managing stock in alignment with shelf life is vital to prevent waste and financial loss.
4. Strategic Sourcing Partnerships
Creating strategic partnerships with suppliers can lead to long-term benefits. By collaborating closely, manufacturers can negotiate favorable pricing, secure priority in times of shortages, and even receive technical support or innovations. For example, forming long-term contracts with suppliers of LR-grade chemicals like oxalic acid or phosphoric acid ensures steady supply at predictable costs, allowing you to plan production and pricing strategies more effectively.
Partnering with logistics providers is also crucial. Reliable transportation ensures timely delivery of materials, and in industries like chemical manufacturing, safety during transport is of paramount importance. Having strong relationships with logistics partners can minimize disruptions and ensure compliance with regulations related to the transport of hazardous materials.
5. Implementing Technology and Automation
Technology plays a transformative role in strengthening supply chains. Supply chain management software offers better visibility, tracking, and control over the movement of raw materials. Blockchain technology can provide a tamper-proof, transparent way of tracking materials from suppliers to manufacturers, reducing the chances of fraud or discrepancies.
In addition, using automation for tasks like order processing, supplier communication, and inventory management can drastically reduce errors and enhance efficiency. Automated systems can predict material needs, reorder when levels are low, and track shipments, enabling businesses to focus on core production activities without worrying about raw material shortages.
6. Building Resilience with Risk Management
Risk management is an essential component of any supply chain strategy. Manufacturers should proactively identify potential risks—such as economic fluctuations, transportation delays, or environmental impacts—and develop mitigation strategies. For example, maintaining safety stock or securing alternative suppliers for critical materials can help offset supply chain disruptions.
Conducting regular audits of the supply chain can also reveal vulnerabilities. For industries that depend on raw materials like LR-grade chemicals, having backup suppliers, well-defined contingency plans, and alternative transportation routes can mean the difference between a minor hiccup and a major production shutdown.
7. Sustainability and Ethical Sourcing
Sustainability is becoming an increasingly important aspect of supply chain management. Businesses are under growing pressure to ensure that their raw materials are sourced in an environmentally friendly and socially responsible manner. For chemical manufacturers, this might mean choosing suppliers that follow eco-friendly production processes or use renewable energy sources.
Ethical sourcing ensures that materials are obtained without exploiting workers or causing harm to local communities. Building a transparent supply chain that adheres to these principles not only improves a company’s reputation but also aligns with global efforts to reduce environmental impact.
Conclusion
Building a strong supply chain for raw materials is a multifaceted process that requires strategic planning, proactive risk management, and close partnerships with suppliers and logistics providers. For manufacturers, especially in industries dealing with chemicals, metals, or raw agricultural products, the reliability of the supply chain directly impacts production efficiency, product quality, and overall profitability.
By focusing on supplier diversification, inventory management, technology integration, and sustainability, companies can build a resilient supply chain that not only supports production but also enhances competitiveness in the global marketplace.